Products Description
SiC (silicon carbide) power devices can effectively meet the requirements of high efficiency, miniaturization, light weight, and high power density of power electronic systems due to their high temperature resistance, high voltage resistance, and low switching loss. It has been sought after by new energy vehicles, photovoltaic power generation, rail transit, smart grid and other fields.
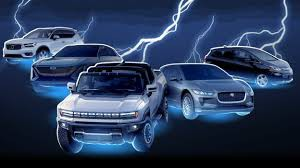
In the field of vehicles, the significant advantages of SiC power devices in energy conversion efficiency can effectively increase the cruising range and charging efficiency of electric vehicles. In addition, SiC devices have lower on-resistance, smaller chip size, and higher operating frequency, which can make electric vehicles adapt to more complex driving conditions. With the improvement of SiC yield and the reduction of cost, the installed capacity of SiC power devices in new energy vehicles will increase significantly, and the demand for SiC power devices in vehicles will also usher in a leapfrog development.
At present, in terms of the global industrial layout of SiC, the United States, Europe, and Japan have formed a three-power situation. However, compared with the first-generation and second-generation semiconductor materials, the global third-generation semiconductor industry is still in the early stage of development, and the gap between the domestic and mainstream SiC industry not big,it provides an opportunity for the domestic three-and-a-half-generation industry to overtake on a bend and enter the high-end industry chain of semiconductor components.
High temperature reverse bias test of SiC power devices:
1. The role of high temperature reverse bias test
The high temperature reverse bias test is to simulate the device working at the highest reverse bias voltage or specified reverse bias voltage in static or steady state mode to study the life simulation of the device under bias conditions and temperature over time. Even some manufacturers will use it as the core test of the first or second screening.
2. Test conditions for high temperature reverse bias
The main test standards for high temperature reverse bias of discrete devices include MIL-STD-750 method 1038, JESD22-A108, GJB 128A-1997 method 1038, AEC-Q101 table 2 B1 item, etc.Various standards have made clear definitions in terms of test temperature, reverse bias voltage and electrical parameter tests, and the test methods and principles are not much different. Among them, the requirements of the automotive regulations are the most stringent , run 1000h under 100% reverse bias voltage.
For SiC power devices, the maximum rated junction temperature is generally above 175°C, and the reverse bias voltage has exceeded 650V. Higher temperature and stronger electric field accelerate the diffusion and migration of mobile ions or impurities in the passivation layer.In this way, device abnormalities can be detected in advance, and the reliability of the device can be verified to a greater extent.
3. Process monitoring of high temperature reverse bias test of SiC power devices
The high-temperature leakage current of SiC diodes is generally 1-100 μA, while the leakage current of SiC diodes during high-temperature reverse bias tests is usually relatively small, at the level of 0.1-10 μA. Leakage can also increase over time if the device is defective. This requires a real-time, high-precision leakage monitoring system to provide monitoring data of leakage current throughout the test cycle to observe the test status of the device.
4. How to pass the high temperature reverse bias test?
The high-temperature reverse bias test mainly examines the material, structure, and packaging reliability of the device, which can reflect the weakness or degradation effect of the device's edge terminal, passivation layer, and interconnect structure.
Therefore, whether a power device can pass the high-temperature reverse bias test should consider risks from the product design stage, and comprehensively consider the aging effects of electric field and high temperature on materials, structures, and passivation layers. The actual application environment factors require integrated management and control of material selection, structure construction design, and improve the yield rate.